Relentless Protector: George Harmer
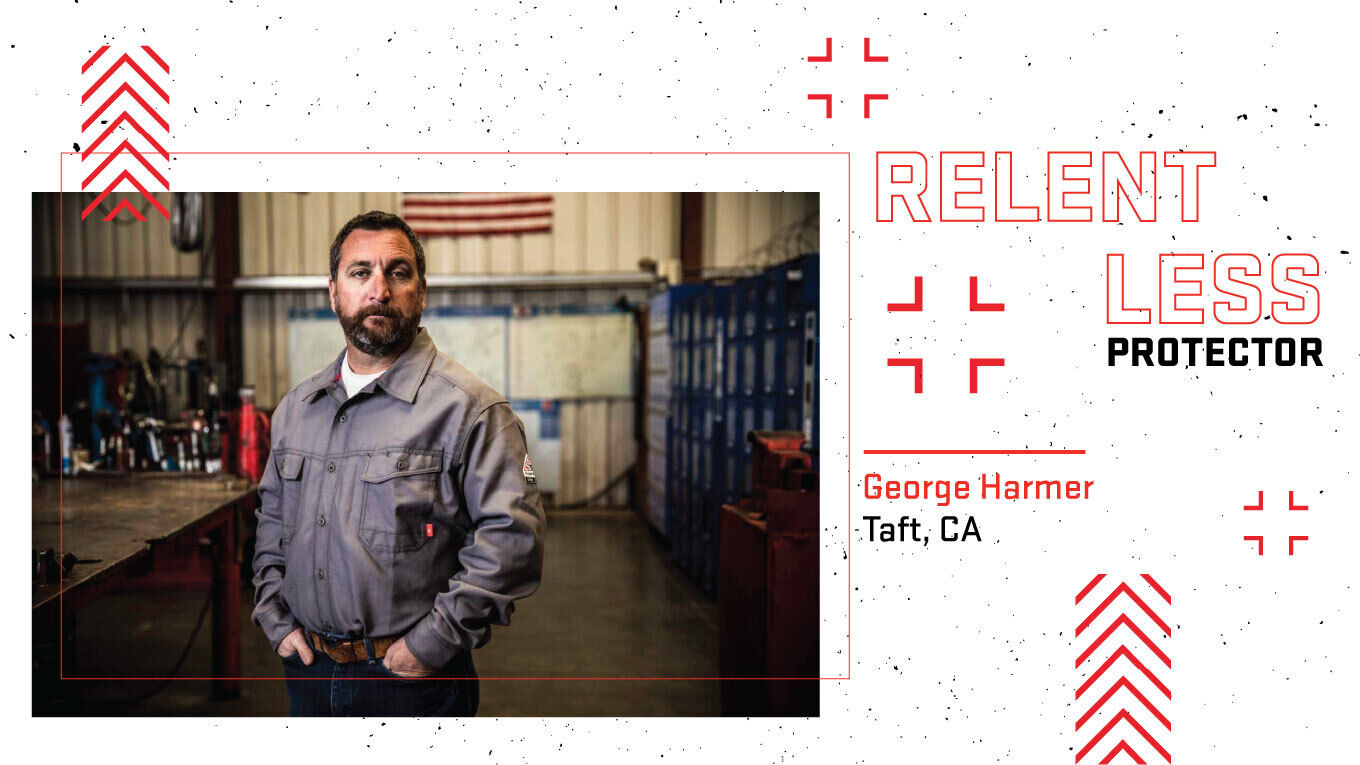
ABOUT GEORGE
George Harmer is the Safety Director for General Production Service (GPS) where he’s been for the last 13 years. He has spent over 25 years in the oil and gas industry starting out at an entry level position and ultimately working into safety and risk management. Currently George oversees a team of 15 safety professionals responsible to over 500 employees. Utilizing a variety of innovative solutions GPS is recognized as a “world-class” organization with their business partners.
Recently, George sat down for a Zoom chat with his longtime friend and Bulwark Business Development Manager, Rick Fisher. They talked about being a Safety Manager, what it means to be in charge of other people’s safety, and how Bulwark helps empower GPS to protect their employees. Watch the full interview above, or check out the highlights below.
INTERVIEW HIGHLIGHTS
RF: Tell me what a given day looks like for a safety director at GPS?
GH: No day is the same in our business. You know, we have a lot of challenges that could arise every day. So typically you get to the yard, you know, 5:30 in the morning, uh, greet what guys I can see. I like to get here early to greet the workforce. And I feel that greeting the workforce every day shows them that we care. So greeting the workforce, and then I get phone calls all the way up until the last crew comes home every day.
RF: Does it put a strain on your family, George, being in such a tough business [the oil and gas business]?
GH: Um, yeah, I mean, there's a lot of uncertainties, you know, every day that we wake up and go into this field. There's, you know, uncertainty with new regulations that may be coming in on the environmental side, on the health and safety side. So it's always difficult with that uncertainty and then too, the other caveat to this job is being able to go home. You know, your spouse sometimes wants to know how your day went. There are so many things that I deal with on a confidential level, protecting employees. Sometimes that makes it tough, you know, because your spouse wants to talk about your day and you don't have that ability. So that definitely makes it tough. Not having the option to vent, I guess if you would.
RF: So as a safety manager or safety professional, what is the toughest part of your job?
GH: The toughest for sure, part of my job, is having to make that phone call to a family member that someone was hurt. I take it personal. I don't allow any of my other staff to make those phone calls. If somebody didn't go home safe today, I make sure that I call that spouse or family member. Just recently it wasn't even related to General Production’s work. We had an employee commuting to work, and unfortunately he didn't make it to work that day. He was killed in a car accident. The regular, you know, CHPs and some of the other folks that should've made that call took too long, and I couldn't stand by and have a spouse and a son and a daughter wonder where their father is. So I had to go out there and let them know that he was gone. So, you know, I take that very personal, whether they're on the job or this happens off the job, you know, we love our employees and I want to make sure they're taken care of.
RF: Yeah, I'm sorry that you would have to go through that or anybody in your company or their families. Switching gears. George, what is the best part about your job being a safety professional at General Production Service?
GH: Hands down the best part is going out there and [knowing that] the employees know that we care about them. Every year General Production Service has an annual company picnic. Meeting the families, you know, seeing the kids playing out there and having all the families come up to me during that time and say how much they love this company, because of the company loves them. So that's by far the greatest, just intermingling with family members and the company and letting them know how much I care about them.
RF: So I know that safety is a huge part of your job task. Tell me a little bit about your flame resistant apparel program.
GH: We started this program, I want to say back in 2011-ish or 12, that's where we first met. When we started this process, it's been something that's challenging at times. And the reason I say challenging is if you're not hooked up with the right person to help you through this process, you'll be in garments that don't fit the needs to the employees. Like, they're not comfortable. So it was challenging for the first a year and a half before you and I met and we sat down and that's the one thing that I found that helped us out the most is when you came in and sat down with us, it was different. And I say different because you didn't come in and say, this is what you need. You came in and said, what do you need? So for me, that took the challenge out of it.
RF: So when you chose Bulwark as your protective apparel brand, give me some of the most important factors, like environmental heat, comfort. Tell me the things that really mattered most to George Harmer.
GH: Well, the first thing definitely was comfort because if the guys don't—if they're not comfortable—they're not going to wear them properly, or they're not going to wear them at all. The other thing was, you know, we live in California in the Central Valley. Our summers can get unbearable to most folks, you know, just last week we had temperatures up to 109° in areas. So these guys gotta be able to…1. I have to comply with the FR regs. And then 2. I also have to make sure that our guys go home every day. And we comply with the heat on this prevention program that is set forth by Cal OSHA. So they have to be lightweight and breathable for the employees.
RF: So comfort was extremely important to you. Heat stress, having a garment that could breathe and cool the body. And if I remember correctly, you guys were having issues with your older product prior to Bulwark, not withstanding the rigorous strengths of what you guys do. Can you tell me a little bit about that?
GH: Yeah. Durability was a factor in the early times of our FR program. They wouldn't hold up to what we're doing out in the field. When I say we are a heavy wear company—it was amazing when we started working with Bulwark—When I said heavy wear, you brought a team out here and said, show us. No other company [did that]. They all said, “Oh, we understand heavy wear. We have a lot of heavy wear contracts out there.” They didn't have a clue. In well servicing, you're touching metal all day long. We're in high soiled conditions every single day. So these folks early on had to go at these garments so tough [with] high temperatures to wash on, chemicals to get the hydrocarbons out of the uniforms. So it was just destroying the fabric. So that's why we, when you came out, you not only said to us, what do you need? How can we help? You said, what can we produce for you? So working together, I think, came up with one of the best garments and fabrics that's on the market right now, the iQ series®.
RF: What makes you nervous about not only just your FR program, but your [overall] safety program, when you wake up in the morning and think about safety, George?
GH: You know, every day, uh, I go to bed thinking about it and I wake up thinking about it. The first thing I think about is, [is] today the day that someone's not going to do the right thing? You know, we have some mottos around here, it's our brother's keeper. So we want to empower each employee to take care of one another. We tell them, 1. you have an obligation to yourself. [2.] You have an obligation to that guy that's working next to you and an obligation to their family to make sure that they go home safe every day. So you just think, is today the day that someone's not gonna take a stand for safety. So that's why I coach my guys every day to make sure they're out there, coaching those employees to do the right thing. So that's what you worry about every day. And if you don't, you're in the wrong field, you should not be in the safety profession. If you don't think about that every day, and think about the employee's wellbeing, this is the wrong job for you.
RF: It must be a heavy burden. And I appreciate the candor. So you have the right tools. You have the right product. Tell me a little bit about the training that you give your employees on the flame resistant apparel.
GH: You know, every year we have an annual core training that we bring our employees in to go over our core values. Those are safety values. Those are corporate values. Those are our customer values. So to bring them in for that, and then to show them how to care for the garment out in the field. Thankfully our folks right now don't have to launder them themselves. We actually use a third party to launder our garments, but we do have some supervisors. And now we're taking that next step to give some of our folks the ability to care for their garments themselves. So really just to show them what the garment can do, you know, what it's intended to do. Some folks that we see out in the field—they don't work for our company—they'll have their garments untucked. So our guys will actually tell them, “Hey, you know, the whole purpose of that garment is to protect you in the event of a flash fire. And if you have it untucked, it's not doing what it's designed to do.” So just the training that we give our folks, they're able to go out and express that to other contractors that may be working in the area. So it's an empowering thing.
RF:That's really great to hear. Has Bulwark helped you guys understand the training process behind the flame resistant apparel?
GH:I will say that's an absolute, yes. And it's—I can tell the folks that may be watching this, um, Bulwark folks have been on our property over the last, let's just say nine years, more than a hundred times. That's you coming out, dealing with our folks, going out in the field with us, bringing your research team down here to look at what we're doing. So, absolutely. Bulwark has been not only a help in developing the perfect garment for us, but coming out and showing our employees how much they care about them to produce a garment that would protect them, train the employees. So it's been a wonderful partnership.
GEORGE HARMER'S BULWARK FR FAVORITES